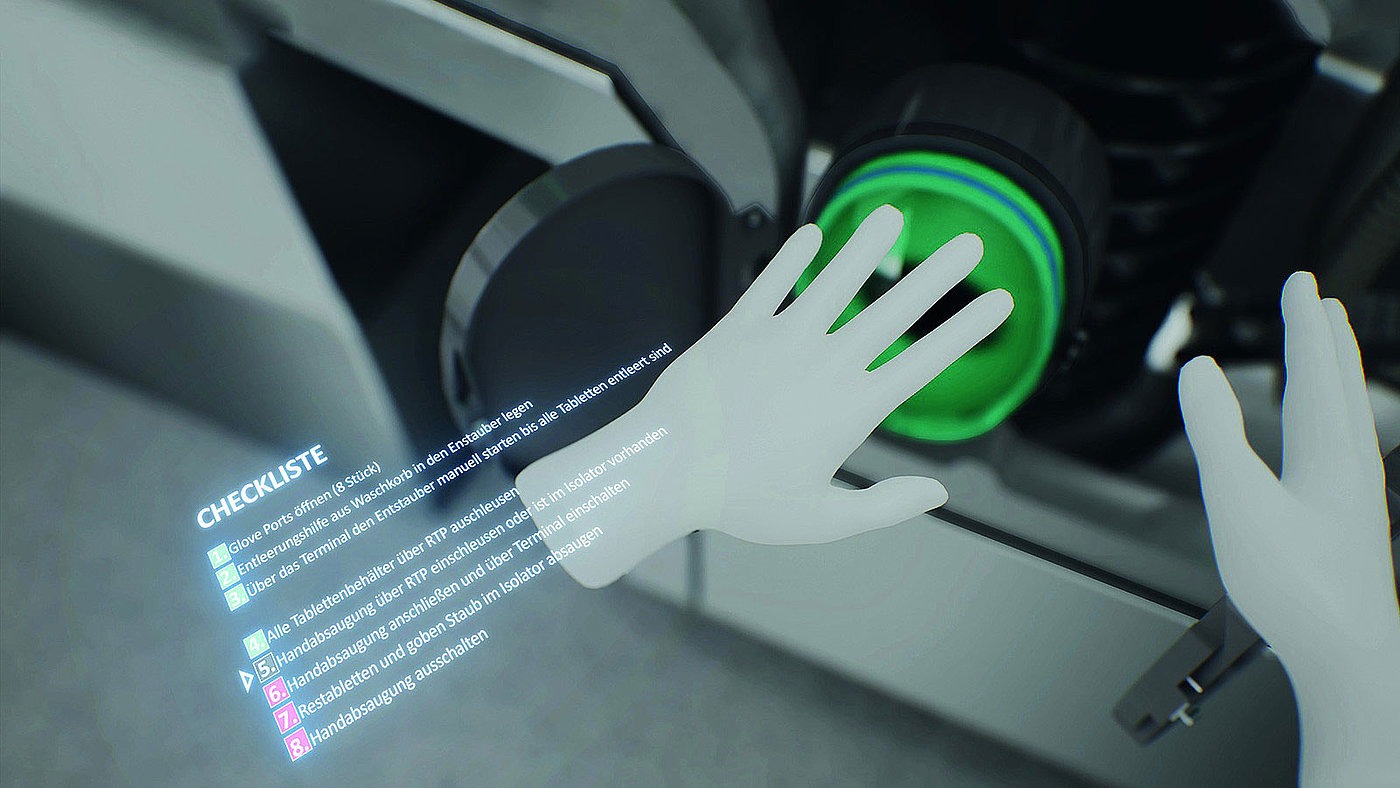
Individual steps can be practiced using a checklist.
As of 2021, around 75 employees in the “Solids Launch Factory” in Ingelheim will be developing new production methods and manufacturing pharmaceuticals for international market launches. 2090i WiP (Wash-in-Place) machines supplied by Fette Compacting will be deployed for the first time to process highly-active ingredients. Thanks to the virtual VRCampus training program, employees are already practicing the unfamiliar steps in the isolator.
VRCampus was developed in collaboration with the Bizzlogic agency and the project was overseen by Tim Klingenhof, Head of Training at Fette Compacting. “We were just planning our training program when Boehringer Ingelheim requested our support. The timing was perfect. This enabled us to cooperate with a user to develop an initial training module,” is how Klingenhof explains how the project got started. Apart from training ahead of commissioning, VRCampus offers Boehringer Ingelheim additional advantages, too: “Virtual training means that the machines are not tied up at a later stage and no costs are incurred for their operation,” according to Klingenhof. “Training can be conducted independent of location which makes the use of VRCampus very flexible. A room measuring 3 by 3 meters, VR goggles, a computer, and our software – that’s it. And employees lose their inhibitions about doing something wrong or even damaging something.”
Process reliability with a high score
Companies benefit from adherence to standardized processes. “Employees often train each other. Although understandable, this also harbors the risk of errors being passed on from one to the other. And these minor changes all add up. VRCampus ensures a consistent training standard,” claims Klingenhof. An additional incentive is offered by gamification elements: on completion of a test, operators receive a certificate and can compare themselves using a high-score list. Martin Döhms, responsible for coach support at Boehringer Ingelheim, was immediately aware of the opportunities: “Our employees experience a working environment in production which is continuously being modernized. Even under the new containment conditions, they still need to be able to handle the process equipment in the isolator. Virtual training enables them to practice handling in the unfamiliar glove ports ahead of actual operation.”
From discovery mode to perfect cleaning
Depending on the learning level, users can familiarize themselves with the machine in “discovery mode” and see into the isolator interior from all angles. During the first training level – and according to instructions and tips provided by avatar “Helmut” – the aim is to remove product residue inside the isolator and work through all steps using a checklist. Helmut Bommrowitz served as a model for the avatar. Fette Compacting is currently planning a training module for a cleaning changeover. Here, too, Helmut is sure to have the right tips to hand.
Please do not hesitate to contact us if you have any queries.